Checking Out the Globe of Steel Stamping: From Layout to Manufacturing
Within the world of production, steel stamping stands apart as a specific and efficient method for shaping metal sheets into various types with exceptional uniformity. From the first layout phase where elaborate patterns materialize to the complex manufacturing procedures, steel stamping is a blend of artistry and engineering. Delving right into this world reveals a complicated interplay of imagination and technical mastery, providing a peek into a realm where innovation meets workmanship.
Background of Steel Stamping
Metal stamping, a widely used manufacturing procedure today, has an abundant background that goes back to ancient times (Metal Stamping). The origins of steel marking can be mapped to ancient worlds such as the Egyptians, who used stamping techniques to decorate fashion jewelry and accessories with detailed designs. In time, steel marking developed, with people like the Greeks and Romans utilizing it for developing coins and attractive products
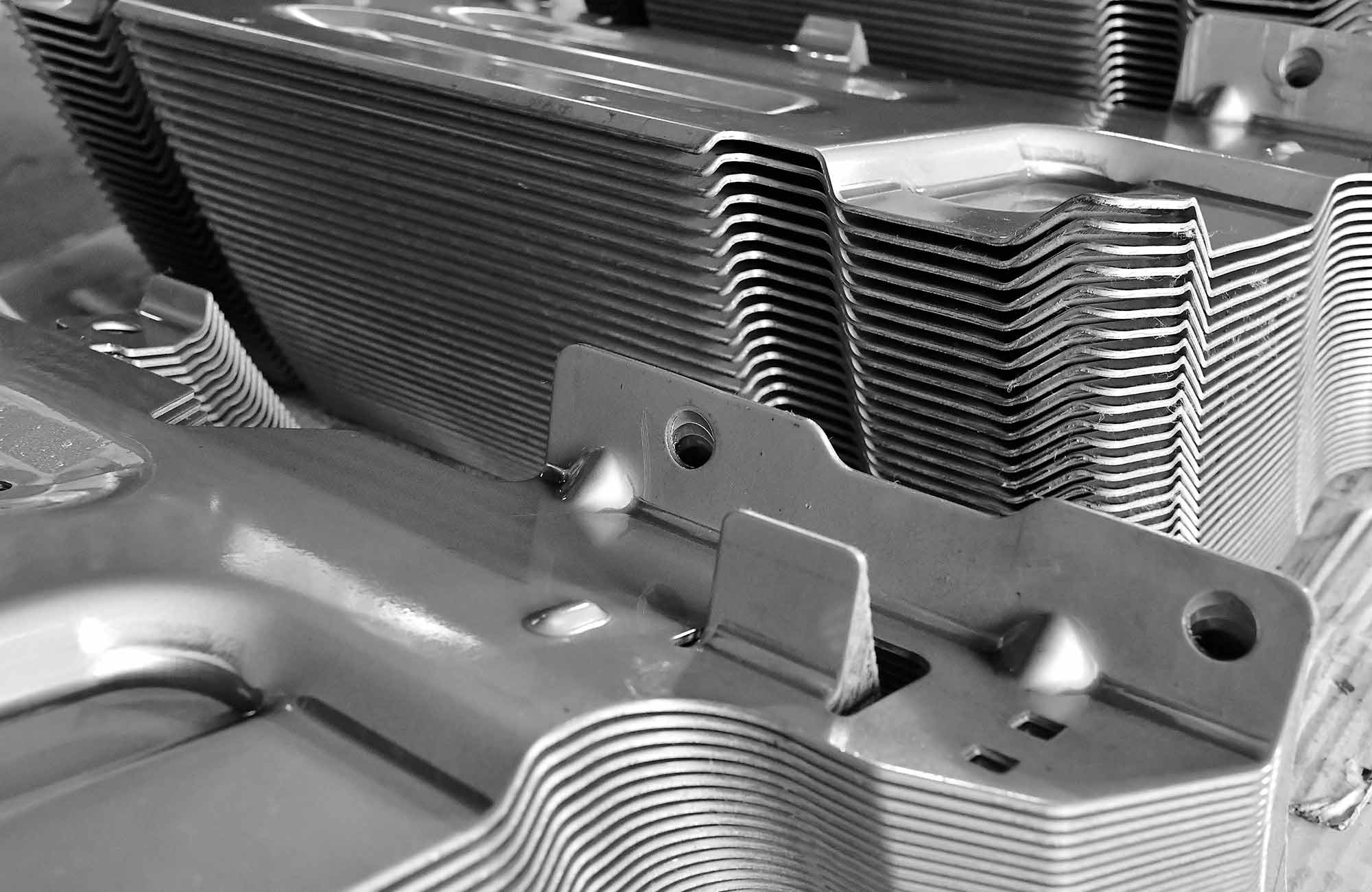
In the 20th century, steel stamping remained to develop with the integration of automation and computer system mathematical control (CNC) technology. These advancements even more raised the performance and accuracy of steel stamping processes, making it a crucial part of modern production throughout sectors such as auto, aerospace, and electronics. Today, steel stamping stays an important production procedure, incorporating practice with development to fulfill the needs of a regularly evolving market.
Layout Considerations and Prototyping
Design considerations in steel stamping consist of material choice, component geometry, tooling style, and manufacturing expediency. Tooling style plays a substantial function in the success of steel stamping jobs, affecting part accuracy, device long life, and manufacturing effectiveness.
Prototyping is a crucial phase in the steel marking procedure that enables engineers to test the design, confirm manufacturability, and make essential changes prior to full-blown production. Prototyping helps recognize possible problems early, conserving time and expenses over time. It also gives a possibility to maximize the layout for performance and top quality. By meticulously considering design elements and using prototyping, suppliers can simplify the steel marking procedure and accomplish high-quality, cost-effective production outcomes.
Tooling and Devices Essentials
Taking into consideration the critical role that tooling layout plays in the success of metal stamping projects, understanding the necessary tools and devices called for is paramount for attaining reliable production results. Components hold the steel in area throughout the stamping process, making sure precision and repeatability. Spending in top quality tooling and equipment not just enhances manufacturing effectiveness yet likewise leads to higher precision, decreased waste, and overall price savings in metal marking operations.
Manufacturing Refine and Quality Control
Efficiently taking care of the manufacturing process and executing durable quality assurance steps are important for guaranteeing the success of metal marking projects. The manufacturing process in steel marking involves a collection of steps that must be carefully worked with to attain ideal results. It begins with the preparation of basic materials, followed by the setup of the stamping tools and tooling. Operators then feed the products into the press, where the stamping operation happens. Throughout this process, it is critical to check the manufacturing line for any problems that might impact the top quality of the stamped components.
Quality control in metal stamping is vital to supply items that fulfill the called for specifications. Examining the more stamped parts at different phases of manufacturing aids recognize any flaws beforehand, avoiding expensive rework or scrap. Strategies such as dimensional examination, aesthetic inspection, and material screening are commonly employed to ensure the quality of the stamped parts. By maintaining strict high quality control criteria, suppliers can support their credibility for providing high-grade steel stamped products.
Applications and Market Insights
In the realm of steel marking, the successful application of manufacturing procedures and high quality control measures straight affects the effectiveness and dependability of different industry applications and gives beneficial insights into the sector's functional characteristics. Steel marking finds widespread application across diverse industries, including automotive, aerospace, electronics, and home appliances. In the vehicle field, metal marking plays a critical role in producing components such as framework, braces, and architectural components with high precision and effectiveness. The aerospace market relies upon metal stamping for producing complex parts like panels, braces, and fittings that fulfill rigid high quality criteria (Metal Stamping). In the electronics industry, metal stamping is used to create precise elements like adapters, terminals, and warmth sinks. In addition, metal marking facilitates the manufacturing of numerous family home appliances, linked here including fridges, washing makers, and ovens, by offering cost-effective options for manufacturing sturdy and complicated components. Comprehending the applications and sector insights of steel stamping is like this important for maximizing production processes and improving product high quality across different markets.
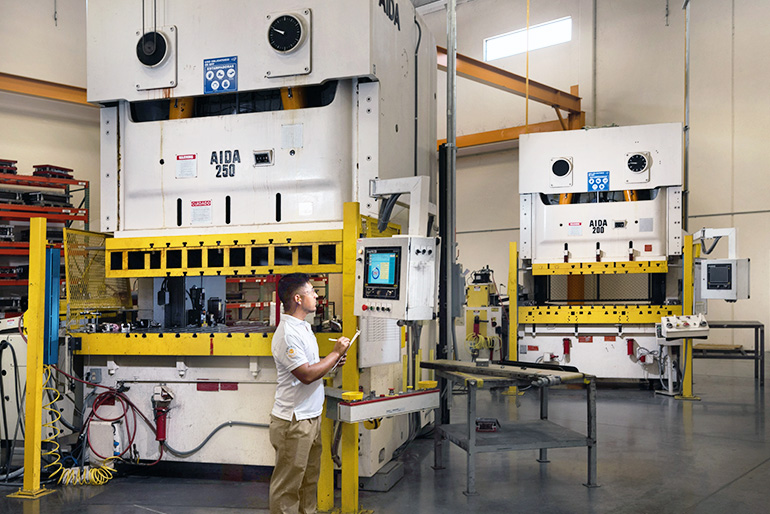
Verdict
Layout considerations, prototyping, tooling, equipment, production procedures, and high quality control are essential elements of steel stamping. With its prevalent applications and industry understandings, metal marking continues to be a functional and efficient production process.